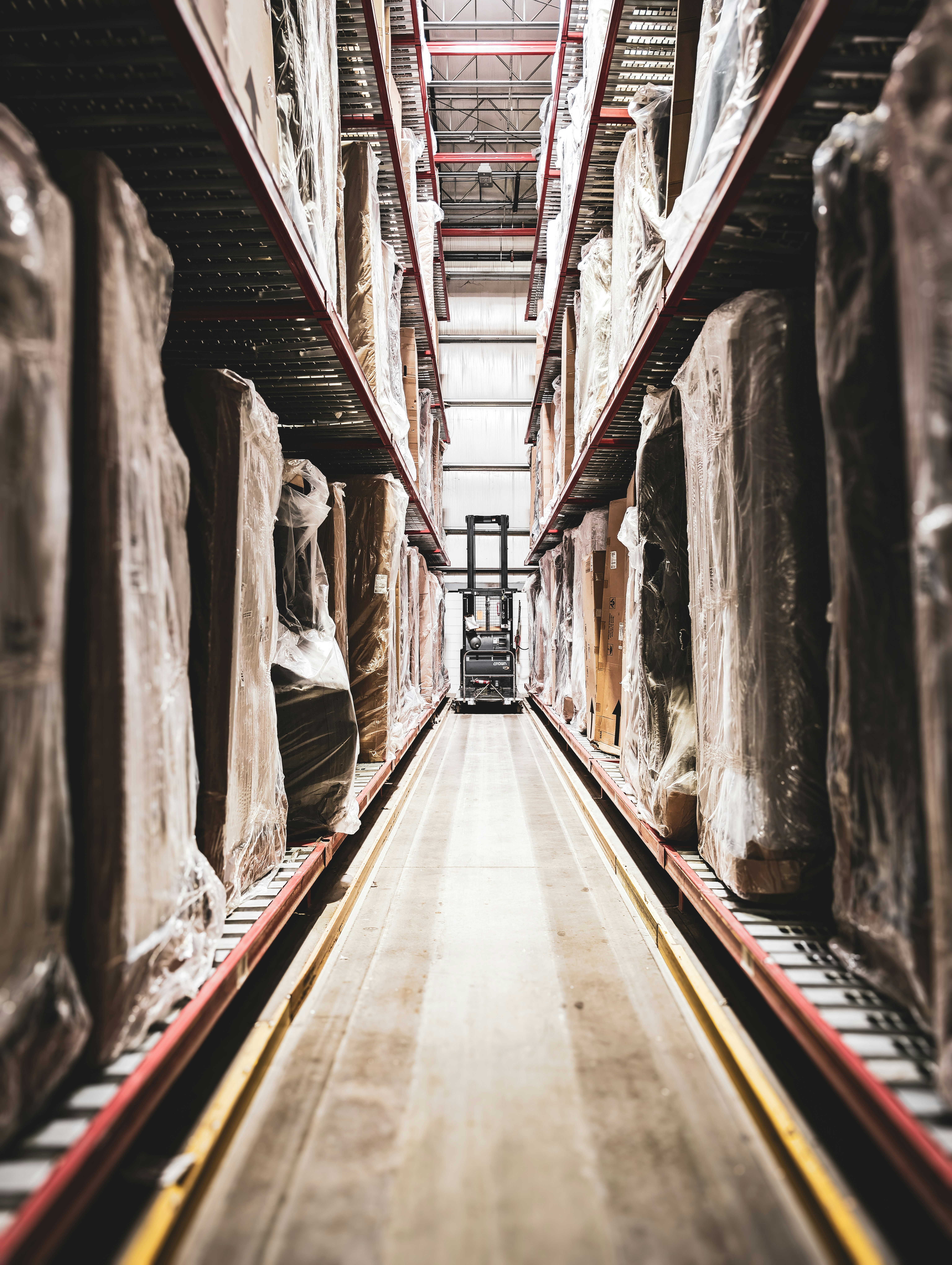
Inventory management is critical to any business that handles physical products. Effective inventory control ensures businesses can meet customer demand without overstocking, which ties up capital and space, or understocking, which results in missed sales opportunities. To maximize stock efficiency, businesses must adopt the proper techniques to streamline operations and improve profitability.
Understanding Demand Forecasting
Demand forecasting is a vital technique in inventory management because it helps businesses predict the amount of stock needed over a certain period. Companies can estimate future demand more accurately by analyzing historical sales data, trends, and seasonal factors. This insight allows companies to prepare for spikes in demand, ensuring they don’t run out of stock when customers need products the most. For example, retailers can stock up on popular items before significant holidays or sales events.
However, demand forecasting goes beyond just looking at past trends. Businesses must also consider market conditions, economic influences, and competitor actions. Transitioning to a more data-driven forecasting approach can improve companies’ ability to adjust to changes in consumer behavior. By doing so, businesses can optimize inventory levels, reducing the risk of overstocking or understocking. This approach is beneficial in industries where demand fluctuates frequently or is affected by external factors.
Implementing Just-In-Time (JIT) Inventory System
Just-In-Time (JIT) inventory is another powerful strategy for managing stock levels. The JIT approach aims to minimize inventory holding costs by only ordering stock when it is needed for production or sales. This method helps reduce the need for large storage spaces and the associated costs. For instance, a company might place orders for materials only when they are close to being needed on the production line, avoiding the need to hold excess stock for long periods.
This technique also encourages better relationships with suppliers, as timely deliveries become crucial to the JIT model’s success. By working closely with suppliers, businesses can ensure that products are delivered right when required, thus maintaining an efficient inventory system. Moreover, JIT inventory helps reduce waste and spoilage, as businesses are not holding perishable goods longer than necessary. While the JIT model offers many advantages, it requires careful coordination and real-time data monitoring to ensure smooth operations.
Utilizing ABC Analysis for Stock Prioritization
ABC analysis is a technique that divides inventory into three categories based on its value and importance. ‘A’ items are the most valuable and essential for business operations, while ‘B’ items are moderately important, and ‘C’ items are less critical. By applying this method, businesses can prioritize stock management efforts on the most crucial products, ensuring they never run out of high-demand or high-value items. This approach can significantly improve stock efficiency as businesses focus on managing the items that most matter.
The main benefit of ABC analysis lies in its ability to optimize inventory storage and management processes. For example, high-value items (A-items) might be given the most attention regarding security, storage space, and order frequency. In contrast, lower-value items (C-items) can be ordered in larger quantities less frequently, reducing overall order processing time. This system saves time and resources and enhances cash flow by focusing efforts on the most profitable goods.
Adopting an Inventory Optimization Strategy
Inventory optimization goes beyond maintaining adequate stock levels—finding the perfect balance between stock availability and cost efficiency. The goal is to ensure businesses carry enough stock to meet customer demands while minimizing excess inventory, which can lead to overstocking costs, storage issues, and obsolete products. An optimized inventory system helps companies maintain a lean operation and improve cash flow by preventing unnecessary purchases or delays in replenishment.
One of the key elements of inventory optimization is setting appropriate reorder points. Businesses can ensure they don’t run out of essential items by determining when to reorder products based on demand, lead time, and stock levels. In addition, it’s crucial to evaluate the sales cycle of different products and adjust stock levels accordingly. For instance, slow-moving products may require less frequent ordering, while fast-moving items might need more regular restocking. With a well-optimized inventory strategy, businesses can minimize stockouts, reduce excess inventory, and improve overall operational efficiency.
Continuous Monitoring and Adjustment
Effective inventory management is an ongoing process that requires continuous monitoring and adjustments. The business landscape constantly evolves, and as demand fluctuates or new products are introduced, companies must be prepared to adapt. Regularly reviewing inventory levels, sales trends, and forecasting methods helps businesses stay on top of their stock management efforts. Additionally, companies can track key performance indicators (KPIs) such as inventory turnover rates, order fulfillment times, and carrying costs to assess the effectiveness of their inventory management system.
By fostering a culture of continuous improvement, businesses can fine-tune their inventory processes and ensure long-term efficiency. Regular adjustments help companies stay competitive and responsive to market changes, improving their ability to deliver the right products at the right time. Inventory management is not a one-time fix; it’s a dynamic process that requires constant attention and refinement to maximize efficiency and reduce costs.